What is PLC? What is its structure? What are its areas of use?
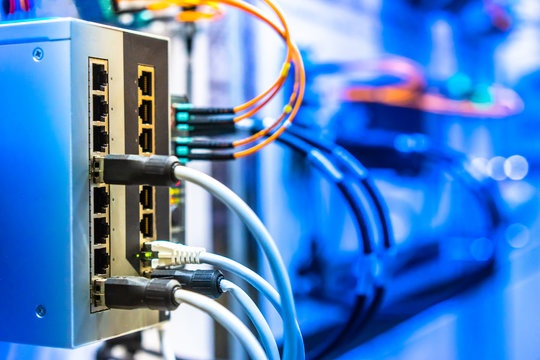
What is PLC?
PLC, an abbreviation of the words Programmable Logic Controller, is a microcomputer that constantly monitors the status of input devices and makes decisions based on a special program to control the status of output devices. It is generally produced for use in industrial environments. Many input and output ports are integrated into the PLC to control and manage processes or systems. In addition, some communication protocols used in industrial application are available in PLC. In addition to the increase in the importance of speed, control, product quality and safety in automatic control units with the development of PLC systems, the creation of new control circuits to manufacture new products, their assembly and elimination by PLC programming instead of changes in the connection apparatus provide businesses with great ease of use and flexibility. Such advantages have led to an increasing need for PLC-based control systems in industrial automation circuits.
What are the usage areas of PLC?
PLCs are generally used in packaging and packaging systems, transportation systems, textile, chemical and automotive industries, cement industry, ventilation and cooling facilities, food industry, etc. It is used in areas. General application areas of PLC are as follows; Sequential Control: One of the most important features of PLC is sequential operation. Therefore, it is close to relay systems. It is generally used in elevator and packaging systems. Motion Control: It is the integration of linear or rotary motion systems in PLC. Generally, Cartesian robots are used in film, rubber, fabric and textile production. Process Control: It is a step where the PLC controls several parameters. This area includes areas such as plastic injection machines and heating ovens, where inspections such as temperature, pressure, flow rate and weight are carried out. Data Management: PLCs can collect data about the systems they control. Then, by comparing this data with reference data in the controller's memory, the data can be transferred to a device to prepare a report. This application is also used in large enterprises that require stocking.
What is the Basic Structure of PLCs?
PLCs are devices used in microprocessor-based automation systems instead of elements such as auxiliary relays, timers and counters used in control circuits. It is possible to solve complex automation problems quickly and safely thanks to these systems.
1. Input memory
They are units that read values such as pressure, level and temperature of the controlled system through sensors, convert the electrical values (input signals) received from elements (sensors) such as buttons and limit switches into logical values and transfer them to the CPU (Input Display Memory). Depending on their make and model, PLCs may have digital only or both digital and analog input units. The input memory of the PLC is designed as non-contact inputs. Signals coming to the PLC from other elements are electrically isolated with an optocoupler. PLC input signal voltages are generally produced as DC 24V. When an input is polled by the PLC, the voltage at the input terminal of the controller is measured. Since they are digital inputs, they only have two signal values, “1” or “0”. Signal changes at the input terminal vary depending on the type of module .
2. CPU (Central processing unit)
Central processing units constitute the brain part of PLC systems. It is a multiprocessor system that replaces the CPU, control relays, counters, timers, and sequencers. When processing digital data, PLC processors are used for calculations, measurement, control and recording operations, as well as simple processing of signals in binary code. The CPU accepts input data from various sensing devices, executes the stored user program from memory, and sends appropriate commands to the control device. This unit, the CPU (Central Processing Unit), loads the logic values transferred from the input unit into its memory and executes the program according to these values and transfers them to the output unit. Just as the brain of computers is the CPU, the CPU also plays the role of brain in PLCs. There are CPU models on the market that will meet different expectations. These models differ from each other with values such as the number of counters, the number of timing, memory retention, number of memory elements, and processing speed. It consists of memory structures such as the central processing unit, program memory, basic software, user program and data memory. Program memory contains all instructions that take the name of the program. The basic software and user program memory of the central processing unit is located in this area.
3. Output memory
These units are units that convert the logic values (0-1 or analog signals) written to the output image memory by the CPU into electrical signals. It is equipped to drive control components in the system such as contactors, relays and solenoids. The output unit can be relay, transistor or triac output.
4. PLC Communication Modules
Communication modules such as Profibus, Profinet, RS232, RS485 and GPRS are used to communicate with PLCs or other devices. Profinet connection cable is used for S7-1200 model PLCs to communicate with the computer. Profinet cable is immune to noise and supports data transfer up to 10/100 Mbit per second.
If you liked my article, I am waiting for your comments and votes. Finally, don't forget to check out my past articles to learn more.
What is Modbus TCP?
What is ProfiBUS/ProfiNET?
What is CanOPEN and CanBUS? (Controller Area Network)
What are PLC programming languages (Part-2)
What are PLC programming languages (Part-1)
What is SCADA?
What is HMI Panel/Display?
What is EtherCAT?